一、管線鋼概述
1、簡介
管線要求含碳量較低,而靠提高錳含量,添加鈮、鈦、釩、鉬等微量元素來保證其強度。對于管線鋼,除了要求強度、塑性指標外,對于韌性指標的要求是它的一個突出特點,包括了鋼板的沖擊功、沖擊轉變溫度和焊接熱影響區與焊接金屬的韌性指標。此外,還有應變時效、可焊性、應力腐蝕等指標要求。
2、管線鋼類型
管線鋼可分為高寒、高硫地區和海底鋪設三類。從油氣輸送管的發展趨勢、管線鋪設條件、主要失效形式和失效原因綜合評價看,不僅要求管線鋼有良好的力學性能(厚壁、高強度、高韌性、耐磨性)還應具有大口徑、可焊接性、耐嚴寒低溫性、耐腐蝕性(CO2)、抗海水和HIC(腐蝕環境下由氫誘導所致的裂紋)、SSCC(低溫環境下由硫導致的裂紋)性能等。這些工作環境惡劣的管線,線路長,又不易維護,對質量要求都很嚴格。
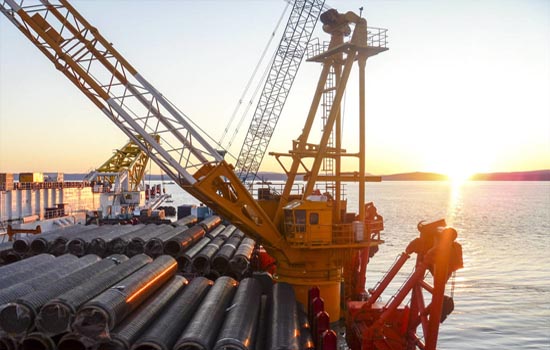
3、管線管的生產工藝
目前在國內管線鋼的生產工藝主要有:常規半連續熱連軋、CSP連鑄連軋、中厚板機組、爐卷機組。
(1)半連續軋機:包括1機架爐卷軋機及5機架精軋機。在半連續軋機上,鋼帶在精軋道次所經歷的熱軋從鋼帶的一端到另一端實質上是恒定的。在精軋機上道次間的
時間通常少于3s。
(2)CSP連鑄連軋:在CSP生產線上對含有鈮、釩、鈦復合微合金化的低碳錳鋼,采用合適的控軋控冷和卷取工藝,可以保證鋼的力學性能和顯微組織符合現代X60管線鋼的技術要求,符合現代管線鋼發展趨勢。我國CSP連鑄連軋生產線目前已開發到了X60管線鋼,而美國及國外其它CSP生產廠已經開發和生產了高牌號管線鋼X60、X65乃至X70。
其工藝特點是連鑄薄板坯存在中心偏析,消除連鑄薄板坯中心偏析是進一步進步管
線鋼質量的關鍵技術題目。
(3)中厚板機組:主要生產寬厚板,用于直縫埋弧焊管的生產,直縫埋弧焊管質量可靠,廣泛應用于油氣高壓輸送主干線上。
(4)爐卷軋機:爐卷軋機包括一架往復式粗軋機及一架4輥往復精軋機。在精軋機兩邊的輸送線上安裝了兩臺熱卷軋機。輸出輥道通常包括一套層流冷卻系統和一個卷取站。在爐卷軋機上,鋼帶整個長度上的熱機械歷史明顯變化,尤其是在微合金化鋼生產中,將強烈影響精軋機上產生的再結晶程度、晶粒長大及析出,并且導致整個帶鋼長度上終極顯微組織和性能的劇烈變化。其工藝特點是投資本錢相對低。
目前國外在爐卷生產線上已生產出X70、X80級管線鋼,主要生產廠家為IPSCO,該廠具有超過35年操縱爐卷軋機的經驗,近年來已對550MPa級Ⅱ類的1219mm直徑及12.0mm壁厚管線鋼進行了產業生產。
4.焊接鋼管按工藝區分
主要有電阻焊(ERW)、螺旋埋弧焊(SSAW)和直縫埋弧焊(LSAW)三種工藝。這三種工藝生產的焊管,因其原料、成型工藝、口徑大小以及質量的不盡相同,在應用領域里各有定位。
(a)直縫電阻焊管(ERW)
電阻焊管是我國最早生產、應用范圍最廣、生產機組最多(2000余家)、產量最高(占焊管總產能的80%左右)的鋼管品種,產品規格為φ20~610mm,在國民經濟建設中發揮了重要作用。ERW219-610mm機組自20世紀80年代以來,約有30余套是從國外引進的較先進技術。經過多年生產實踐,裝備技術水平又有較大進步,產品質量也在不斷改善。因其投資少,見效快,應用范圍廣而發展迅猛。隨著板材CSP生產工藝的發展,為其提供了低本錢、質量可靠的原料,并為其今后進一步發展創造了良好的條件。這部分產品已由流體輸送、結構領域向無縫管應用領域的油井管、管線管發展。其典型生產工藝流程應為:板帶原料→原料預處理→冷彎成型→焊接→焊縫熱處理→焊縫(管體)探傷→精整→成品焊管。
(b)螺旋埋弧焊管(SSAW)
螺旋埋弧焊管設備投資較少,因采用價格較低的窄帶(板)卷連續焊接生產大口徑(φ1016~2400mm)焊管,生產工藝簡單、運行用度低,具有低本錢運行上風。目前,我國油氣輸送螺旋焊管已形成了以石油系統所屬鋼管廠為主的基本格式。采用低殘余應力成型和管端機械擴徑等先進技術,經過嚴格質量控制的螺旋焊管在質量上可與直縫焊管相媲美,我國西氣東輸等油氣長輸管道工程中獲得了廣泛應用,是我國油氣長輸管道工程采用的主要管型。其目前的產能已經能夠滿足我國油氣長輸管道工程建設的需要,并已大量出口。
(c)直縫埋弧焊管(LSAW)
直縫埋弧焊在我國事較晚發展起來的先進制管技術,過往主要采用UOE技術制造。
近年來漸進式JCOE在我國和全世界逐漸成為另一種新的主流技術。直縫埋弧焊管質量可靠,廣泛應用于油氣高壓輸送主干線上。該焊管機組由于投資相對較大,使用的原材
料為本錢較高的單張寬厚板,工藝較復雜,生產效率低,產品本錢較高。
由于我國高壓油氣輸送管線每年需要大中口徑焊管100萬t左右,主要采用螺旋焊管,直縫埋弧焊管將作為螺旋焊管的補充,主要應用于螺旋焊管機組不能生產的大壁厚鋼管(17.5mm以上)和彎管用母管,其用量受到一定限制
目前,我國油氣輸送所使用的管線管主要由石油自然氣團體公司的6個焊管廠生產,它們是寶雞石油鋼管廠、貴陽石油鋼管廠、華北石油鋼管廠,遼陽石油鋼管廠,沙市石油鋼管廠,勝利石油鋼管廠等,總設計生產能力約為120萬t左右。生產的油氣管以螺旋焊管和高頻直縫焊管為主,而管徑大、管壁厚的直縫埋弧焊管的生產在我國時間較短。2000年,我國第一條大口徑直縫埋弧焊管生產線在番禺珠江鋼管公司建成,此生產線從澳大利亞引進,可生產厚壁大口徑長輸管線鋼管,鋼管外徑457~1800mm,特殊規格可達3000mm,壁厚4.5~37mm,特殊規格還可增厚,單管最長可達12m。但生產這種焊
管所需管線用寬厚鋼板目前基本還需依靠進口。近日,日本住友金屬和住友商事又與中國石油自然氣團體公司(CNPC)下屬的寶雞鋼管廠合作生產石油自然氣用中徑焊接鋼管,主要生產油氣輸送管線的支線用焊管,產量可由目前的5萬t進步到2~3年后的12萬t。
5、管線鋼的發展趨勢
油氣管道特別是天然氣管道發展的一個重要趨勢是采用大口徑、高地、壓富氣輸送、高寒和腐蝕服役環境、海底管道厚壁化及選用高級別管材。考慮到管道的結構穩定性和安全性,還需增加管壁厚度和進步管材的強度,因此用作這類輸送管的管線鋼都向著厚規格和高強度方向發展。采用高壓輸送和高強度管材,可大幅度節約管道建設成本。目前,輸氣管道的設計和運行壓力已達20MPa,有些管道甚至考慮采用更高的壓力。隨著管道輸送壓力的不斷提高。管線鋼管也迅速向高鋼級發展。因此對鋼材質量要求也日益苛刻,在成分和組織上要求鋼材向著“超高純、超均質、超細化”方向發展。
由于自然氣的可壓縮性,因而輸氣管的輸送壓力要較輸油管為高。近年來國外多數輸氣管道的壓力已從早期的4.5~6.4MPa進步到8.0~12MPa,有的管道則達到了14~15.7MPa,從而使輸氣管的鋼級也相應地進步。目前,國外的大口徑輸氣管已普遍采用X70鋼級,X80開始進進小規模的使用階段,X100也研制成功,并著手研制X120。
21世紀是我國輸氣管建設的高峰時期。“西氣東輸”管線采用大口徑、高壓輸送管的方法。這條管線全長4167km,輸送壓力為10MPa,管徑為1016mm,采用的鋼級為X70、厚度為14.6mm,20℃的橫向沖擊功為≥120J。這一鋼級、規格、韌性級別目前國內已經生產,并且質量達到國際水平。因此,生產這種規格的高強度、高韌性管線鋼對我國今后采用國產管線鋼生產大口徑、高壓輸氣管具有十分重大的戰略意義。
大口徑高壓輸送及采用高鋼級管材是國際管道工程發展的一個重要趨勢:
(1)國內對管線用鋼的需求以X70級為主,新線目標定位在X80級熱軋寬鋼帶和X100級寬厚板的生產,以適應目前10MPa和近期14MPa以上輸送壓力的設計。
(2)今后輸送的自然氣不再是經脫水、脫H2S處理的“甜氣”,而將是未經處理的“富氣”(PH2S≤300Pa),為此必須進步管線用鋼的抗氫致開裂和抗H2S應力腐蝕的性
能。
(3)國內已具有70萬t以上螺旋焊管的制管能力,但大口徑直縫埋弧焊管的產能和質量還不能滿足工程的需求,繼續部分進口成品管將不可避免。從研發基礎和生產技術的難度而言,具有優質的抗H2S應力腐蝕性能的高強度等級管線用鋼的開發應當列為科技攻關的重中之重。
二、技術要求
1、性能要求
現代管線鋼屬于低碳或超低碳的微合金化鋼,是高技術含量和高附加值的產品,管線鋼生產幾乎應用了冶金領域近20多年來的一切工藝技術新成就。目前管線工程的發展趨勢是大管徑、高壓輸送、高冷和腐蝕的服役環境、海底管線的厚壁化,因此目前對管線鋼的性能要求主要有以下幾方面:
(1)高強度。管線鋼的強度指標主要有抗拉強度和屈服強度;在要求高強度的同時,對管線鋼的屈強比(屈服強度與抗拉強度)也提出了要求,一般要求在0.85-0.93的范圍內。
(2)高沖擊韌性。管線鋼要求材料應具有足夠高的沖擊韌性(起裂、止裂韌性)。對于母材,當材料的韌性值滿足止裂要求時,其韌性一般也能滿足防止起裂的要求。
(3)低的韌脆轉變溫度。嚴酷地域、氣候條件要求管線鋼應具有足夠低的韌脆轉變溫度。DWTT(落錘撕裂試驗)的剪切面積已經成為防止管道脆性破壞的主要控制指標。一般規范要求在最低運行溫度下試樣斷口剪切面積≥極85%。
(4)優良的抗氫致開裂(HIC)和抗硫化物應力腐蝕開裂(SSCC)性能。
(5)良好的焊接性能。鋼材良好的焊接性對保證管道的整體性和焊接質量至關重要。
管線鋼的發展最顯著的特征之一就是不斷降低鋼中的C含量,隨著C含量的降低,鋼的焊接性得到明顯的改善。添加微量鈦Ti,可抑制焊接影響區韌性的下降,達到改善焊接性能的目的。
這其中難點和重點是高韌性。隨著石油、天然氣輸送的不斷發展,對石油管線鋼性能的要求不斷提高,尤其是對韌性要求的提高。這些性能的提高就要求把鋼材中雜質元素C、S、P、0、N、H含量降到很低的水平。高強度、高韌性是通過控冷技術得到金相組織來保證的,同時應降低鋼中碳的含量和盡可能去除鋼中的非金屬夾雜物,提高鋼的純凈度。輸送酸性介質時管線鋼要抗氫脆,要求H含量低于0.0002%;對于鋼中的夾雜物,最大D小于100μm,并要求控制氧化物形狀,消除條形硫化物夾雜的影響。
2、各種元素在管線鋼中的作用與控制
高級管線鋼各成分的作用及其控制為滿足管線鋼高強度、高韌性、良好的焊接性能及抗HIC、SCC性能的要求,除了采用合理的冶金技術以外,還要嚴格控制管線鋼的成分。
(1)管線鋼中碳的作用與控制
碳是增加鋼的強度的有效元素,但是它對鋼的韌性、塑性和焊接性有負面影響。
降低碳含量可以改善脆性轉變溫度和焊接性極地管線和海洋管線對低溫韌性、斷裂抗力以及延性和成形性的需要,要求更低的含碳量。對于微合金化鋼,低的碳含量可以提高抗HIC的能力和熱塑性,按照API標準規定,管線鋼中的碳通常為0.025%一0.12%,并趨向于向低碳方向或超低碳方向發展。在綜合考慮管線鋼抗HIC性能、野外可焊性和晶界脆化時,最佳C應控制在0.01%一0.05%之間。
(2)管線鋼中錳的作用與控制
為保證管線鋼中低的含碳量,通常是以錳代碳,Mn的加入引起固溶強化,用錳來提高其強度。錳在提高強度的同時,還可以提高鋼的韌性。但如果錳含量過高對管線鋼的焊接性能造成不利影響,有可能導致在管線鋼鑄坯內發生錳的偏析,且隨著碳含量的增加,這種缺陷會更顯著。因此根據板厚和強度,管線鋼中錳的加入量一般是1.1%-2.0%。
(3)管線鋼中硫的作用與控制
硫是管線鋼中影響抗HIC能力和抗SSC能力的主要元素。隨著硫含量的增加,HIC敏感性顯著增加;只有當S小于0.0012%時,HIC明顯降低。值得注意的是硫易與錳結合生成MnS夾雜物,當MnS夾雜變成粒狀夾雜物時,隨著鋼強度的增加,單純降低硫含量不能防止HIC。如X65級管線鋼,當硫含量降到20ppm時,其裂紋長度比仍高達30%以上。
管線鋼中硫(S)元素對鋼材的影響:硫還影響管線鋼的沖擊韌性,硫含量升高沖擊韌性值急劇下降。
管線鋼中硫的控制通常是在爐外精煉時采用噴粉、真空、加熱造渣、喂絲、吹氣攪拌進行,實踐中常常是幾種手段綜合使用。此外,條狀硫化物是產生氫致裂紋的必要條件,對鋼水進行鈣處理將其改變為球形,可降低其危害。
(4)管線鋼中磷的作用與控制
由于磷在管線鋼中是一種易偏析元素,在偏析區其淬硬性約為碳的二倍。由二倍磷含量與碳當量(2P+Ceq)對管線鋼硬度的影響可知:隨著2P+Ceq的增加,含碳0.12~0.22%的管線鋼的硬度呈線性增加;而含碳0.02~0.03%的管線鋼,當2P+Ceq大于0.6%時,管線鋼硬度的增加趨勢明顯減緩。
在煉鋼整個過程中均可脫磷,如鐵水預處理、轉爐以及爐外精煉,但最終脫磷都是采用爐外精煉來完成。
(5)管線鋼中氫的作用與控制
管線鋼中氫的質量分數越高,HIC產生的幾率越大,腐蝕率越高,平均裂紋長度增加越顯著,自真空處理技術出現以后,鋼中氫已可穩定控制在0.0002%以下。
鋼中氫是導致白點和發裂的主要原因。管線鋼中的氫含量越高,HIC產生的幾率越大,腐蝕率越高,平均裂紋長度增加越顯著。
利用轉爐CO氣泡沸騰脫氫和爐外精煉脫氣過程可很好地控制鋼中的氫含量。采用RH、DH或吹氬攪拌等均可控制[H]≤1.5ppm。
另外,要防止煉鋼的其它階段增氫。采用鋼包和中間包預熱烘烤可以有效降低鋼水的吸氫量。連鑄過程中,在鋼包和中間包系統中對保護套管加熱和同一保護套管的反復使用可明顯降低鋼液的吸氫量。
(6)管線鋼中氧的作用與控制
鋼中氧含量過高,氧化物夾雜以及宏觀夾雜增加,嚴重影響管線鋼的潔凈度。鋼中氧化物夾雜是管線鋼產生HIC和SSCC的根源之一,對鋼的各種性能都起著有害的作用,尤其
是當夾雜物直徑大于50μm后,嚴重惡化鋼的各種性能。為了防止鋼中出現直徑大于50μm(10 m)的氧化物夾雜,減少氧化物夾雜數量,一般控制鋼中氧含量小于0.0015%。
采用爐外精煉可獲得較低的氧含量,國外許多廠家經爐外精煉處理后成品鋼中T[0]最低可達5ppm(10°%)的水平。
另外,由于耐火材料供氧,鋼水在運輸和澆注過程中應盡量減少二次氧化。通過改進以及選擇良好的中間包覆蓋渣和連鑄保護渣,取得較好的效果。目前工業上已能生產雜質含量小于0.01%的高純鋼,預計到21世紀中葉有可能生產出雜質含量只有百萬分之幾的高純鋼。
(7)管線鋼中銅的作用與控制
加入適量的銅,可以顯著改善管線鋼抗HIC的能力。隨著銅含量的增加,可以更有效地防止氫原子滲入鋼中,平均裂紋長度明顯減少。當銅含量超過0.2%時,能在鋼的表面形成致密保護層,HIC會顯著降低,鋼板的平均腐蝕率明顯下降,平均裂紋長度幾乎接近于零。
但是,對于耐CO2腐蝕的管線鋼,添加Cu會增加腐蝕速度。當鋼中不添加Cr時,添加0.5%Cu會使腐蝕速度提高2倍。而添加0.5%Cr以后,Cu小于0.2%時,腐蝕速度基本不受影響,當Cu達到0.5%時,腐蝕速度明顯加快。
(8)管線鋼中其它元素的作用與控制
化學成分中的碳和鈮是控制鋼板的強度、韌性、可焊性和焊接熱影響區裂紋敏感性及對氫誘裂紋和應力腐蝕裂紋敏感性的主要因素。
微合金元素Nb、V、Ti、Mo在管線鋼中的作用與這些元素的碳化物、氮化物和碳氮化物的溶解和析出行為有關。管線鋼除了以上三種普遍使用的合金元素外,還應根據鋼的性能要求加入其它少量合金元素,例如B、Mo、Ni、Cr、Cu等。
鈮是管線鋼中不可缺少的微合金元素,能改善低溫韌性。API標準中規定的管線鋼鈮含量下限為0.005%,然而實際在鋼中的控制水平都在0.03~0.05%之間,為標準中的下限值的6~10倍。
釩有較高的沉淀強化和較弱的細化晶粒作用,一般在管線鋼設計中不單獨使用釩。管線鋼中加入微量的釩,可以通過增加沉淀硬化效果來提高鋼板的強度。國外實物鋼板中的含釩量多數控制在0.05~0.10%之間,為API標準中的下限值的2.5~5.0倍。
鈦與鋼中的C、N等形成化合物,為了降低鋼中固溶氮含量,通常采用微鈦處理,使鋼中的氮被鈦固定。鋼中加入微量的鈦,可以通過提高提高鋼板強度和韌性的目的,尤其是對提高焊接熱影響區的韌性具有獨特的貢獻。
鉬也是管線鋼中主要的合金元素之一,隨著鉬含量的升高,抗拉強度升高。鋼中鉬有利于針狀組織的發展,隨著鋼中鉬的質量分數增加,針狀鐵素體的含量增加,因而能在極低的碳含量下得到很高的強度。
鋼中加入鈣、鋯、稀土金屬,可以改變硫化物和氧化物的成分,使其塑性降低。采用這種方法,可以使鋼板的各向異性大大減輕,使橫向夏比沖擊功增加一倍,達到或接近縱向夏比沖擊功數值。為了使鋼板各向異性達到最小,稀土與硫的比例控制在2.0左右最為合適。
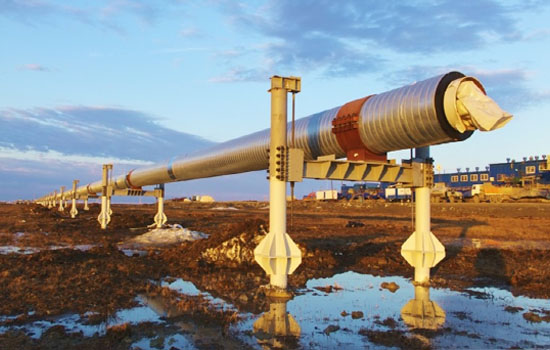
(9)管線鋼中夾雜物的作用與控制
在大多數情況下,HIC(氫誘裂紋)都起源于夾雜物,鋼中的塑性夾雜物和脆性夾雜物是產生HIC的主要根源。分析表明,HIC端口表面有延伸的MnS和Al203點鏈狀夾雜,而SSCC
(硫化物應力腐蝕開裂)的形成與HIC的形成密切相關。因此,為了提高抗HIC和抗SSCC能力,必須盡量減少鋼中的夾雜物、精確控制夾雜物形態。
鈣處理可以很好地控制鋼中夾雜物的形態,從而改善管線鋼的抗HIC和SSCC能力。當鋼中含硫0.002~0.005%時,隨著Ca/S的增加,鋼的HIC敏感性下降。但是,當Ca/S達到一定值時,形成CaS夾雜物,HIC會顯著增加。因此,對于低硫鋼來說,Ca/S應控制在一個極其狹窄的范圍內,否則,鋼的抗HIC能力明顯減弱。
優質管線鋼中有害元素含量的要求
煉鋼 | 應用 | |||
高強度厚壁管 | 低溫管 | 傳輸腐蝕氣體管 | ||
純凈度 |
S<0.005% | O | O | |
S<0.001% | √ | |||
P<0.010% | √ | |||
P<0.005% | ||||
H<1.5×10-% | √ | O | ||
N<40×10-4% | O | O | O | |
鈣處理 | Ca=0.001%~0.0035% | √ | ||
低碳鋼 | C<0.10% | √ | √ | √ |
C<0.005% | ||||
夾雜控制 | O | O | √ | |
中心偏析控制 | O | 0 | √ | |
化學成分精度調整 | √ | √ | √ |
注:√—必不可少的;○—必要的;●—理想的
管線鋼化學成分
牌號 | C | Si | Mn | P | S | Cr | Mo | Ni |
X52 | 0.08 | 0.14 | 0.87 | 0.0080 | 0. 0030 | 0.035 | 0.004 | 0.013 |
X60 | 0.04 | 0.27 | 1.19 | 0.0050 | 0. 0020 | 0.030 | 0.020 | 0.110 |
X70 | 0.05-0.08 | 0.25 | 1.62 | 0.0070 | 0. 0010 | 0.030 | 0.150 | 0.150 |
X80 | 0.04 | 0.30 | 1.80 | 0.0060 | 0.0020 | 0.050 | 0.20 | 0.020 |
X100 | 0.08 | 0.30 | 1.90 | 0.0060 | 0.0010 | 0.25 | 0.030 |
牌號 | Nb | V | Ti | Cu | Al | N | Ca | Ceq |
X52 | 0.022 | 0.005 | 0.008 | 0.015 | <0.03 | 0.0910 | 0.002 | 0.236 |
X60 | 0.049 | 0.040 | 0.015 | 0.230 | 0.034 | 0.0071 | 0.0023 | 0.275 |
X70 | 0.060 | 0.040 | 0.022 | 0.20 | 0.040 | 0.0040 | 0.0010 | |
X80 | 0.045 | 0.005 | 0.015 | 0.200 | 0.0030 | 0.0060 | ||
X100 | 0.050 | 0.015 | 0.17 | 0.03 | 0.0020 |
X70管線鋼典型化學成分(%)及典型力學性能對比
國家或公司 C S i M n Cr Mo Ni Nb V Ti Cu P S寶鋼 | 0.05 | 0.20 | 1.56 | 0.026 | 0.21 | 0.14 | 0.045 | 0.032 | 0.0160.180.0110.003 | |
武鋼 | 0.03 | 0.21 | 1.55 | 0.021 | 0.27 | 0.23 | 0.047 | 0.038 | 0.018 | 0.21 0.0100.002 |
鞍鋼 | 0.03 | 0.27 | 1.56 | 0.025 | 0.25 | 0.13 | 0.057 | 0.040 | 0.021 | 0.140.0050.004 |
日本住友 | 0.006 | 0.15 | 1.62 | 0.020 | 0.01 | 0.20 | 0.035 | 0.050 | 0.022 | 0.28 0.0110.001 |
德國 | 0.007 | 0.27 | 1.57 | 0.060 | 0.01 | 0.03 | 0.040 | 0.0070 | 0.013 | 0.03 0.011 0.001 |
寶鋼 | 14.6 | 橫向 | 525 | 644 | 37.0 | 341 | 0.82 |
武鋼 | 14.6 | 橫向 | 539 | 659 | 42.0 | 402 | 0.82 |
2、直縫埋弧焊管(JCOE)
直縫埋弧焊(LSAW)直縫埋弧焊在我國是較晚發展起來的先進制管技術,過往主要采用UOE技術制造。近年來漸進式JCOE在我國和全世界逐漸成為另一種新的主流技術。直縫埋弧焊管質量可靠,廣泛應用于油氣高壓輸送主干線上。該焊管機組由于投資相對較大,使用的原材料為本錢較高的單張寬厚板,工藝較復雜,生產效率低,產品本錢較高。
◆JCOE:JCOE直縫雙面埋弧焊管該生產線為中國首條大口徑直縫雙面埋弧焊管生產線
生產線采用芯軸旋轉連續J-C-O成型的工藝,速度快,質量高,成型應力分布均勻,管體形狀規則。本生產線采用JCOE工廠的標準配置,其特點是產品規格范圍大,變換規格快而簡單,可實現生產范圍內任何尺寸的產品。產品規格直徑:φ406-φ1829mm(16"-72")壁厚:6.0-25.4mm(1/4"-1")標準:API、BS、ASTM、JIS、DIN、GB、ISO、DNV長度:3-12.2m(10'-40)材質:GB/T9711L190-L555(API5LA-X80)
電阻焊(ERW)
電阻焊管是我國最早生產、應用范圍最廣、生產機組最多(2000余家)、產量最高(占焊管總產能的80%左右)的鋼管品種,產品規格為φ20~610mm,在國民經濟建設中發揮了重要作用。ERW219-610mm機組自20世紀80年代以來,約有30余套是從國外引進的較先進技術。經過多年生產實踐,裝備技術水平又有較大進步,產品質量也在不斷改善。因其投資少,見效快,應用范圍廣而發展迅猛。隨著板材CSP生產工藝的發展,為其提供了低本錢、質量可靠的原料,并為其今后進一步發展創造了良好的條件。這部分產品已由流體輸送、結構領域向無縫管應用領域的油井管、管線管發展。其典型生產工藝流程應為:板帶原料→原料預處理→冷彎成型→焊接→焊縫熱處理→焊縫(管體)探傷→精整→成品焊管。
螺旋埋弧焊(SSAW)螺旋埋弧焊管設備投資較少,因采用價格較低的窄帶(板)卷連續焊接生產大口徑(φ1016~2400mm)焊管,生產工藝簡單、運行用度低,具有低本錢運行上風。目前,我國油氣輸送螺旋焊管已形成了以石油系統所屬鋼管廠為主的基本格式。采用低殘余應力成型和管端機械擴徑等先進技術,經過嚴格質量控制的螺旋焊管在質量上可與直縫焊管相媲美,我國西氣東輸等油氣長輸管道工程中獲得了廣泛應用,是我國油氣長輸管道工程采用的主要管型。其目前的產能已經能夠滿足我國油氣長輸管道工程建設的需要,并已大量出口。
焊接鋼管也稱焊管,是用鋼板!或鋼帶經過卷曲成型后焊接制成的鋼管。焊接鋼管生產工藝簡單,生產效率高,品種規格多,設備投資少,但一般強度低于無縫鋼管。20世紀30年代以來,隨著優質帶鋼連軋生產的迅速發展以及焊接和檢驗技術的進步,焊縫質量不斷提高,焊接鋼管的品種規格日益增多,并在越來越多的領域代替了無縫鋼管。焊接鋼管按焊縫的形式分為直縫焊管和螺旋焊管。直縫焊管生產工藝簡單,生產效率高,成本低,發展較快。螺旋焊管的強度一般比直縫焊管高,能用較窄的坯料生產管徑較大的焊管,還可以用同樣寬度的坯料生產管徑不同的焊管。但是與相同長度的直縫管相比,焊縫長度增加30~100%,而且生產速度較低。因此,較小口徑的焊管大都采用直縫焊,大口徑焊管則大多采用螺旋焊。
低壓流體輸送用焊接鋼管(GB/T3091-2008)也稱一般焊管,俗稱黑管。是用于輸送水、煤氣、空氣、油和取暖蒸汽等一般較低壓力流體和其他用途的焊接鋼管。鋼管接壁厚分為普通鋼管和加厚鋼管;接管端形式分為不帶螺紋鋼管(光管)和帶螺紋鋼管。鋼管的規格用公稱口徑(mm)表示,公稱口徑是內徑的近似值。習慣上常用英寸表示,如11/2等。低壓流體輸送用焊接鋼管除直接用于輸送流體外,還大量用作低壓流體輸送用鍍鋅焊接鋼管的原管。
1.低壓流體輸送用鍍鋅焊接鋼管((GB/T3091-2008)也稱釵度鋅電焊鋼管,俗稱白管。是用于輸送水、煤氣、空氣油及取暖蒸汽、暖水等一般較低壓力流體或其他用途的熱浸鍍鋅焊接(爐焊或電焊)鋼管。鋼管接壁厚分為普通鍍鋅鋼管和加厚鍍鋅鋼管;接管端形式分為不帶螺紋鍍鋅鋼管和帶螺紋鍍鋅鋼管。鋼管的規格用公稱口徑(mm)表示,公稱口徑是內徑的近似值。習慣上常用英寸表示,如1/2、3/4、1、2等。
2普通碳素鋼電線套管1(YB/T5305-2006)是工業與民用建筑、安裝機器設備等電氣安裝工程中用于保護電線的鋼管。
3.直縫電焊鋼管(GB/T13793-2008)是焊絳與鋼管縱向平行的鋼管。用于一般結構用,通常分為公制電焊鋼管、電焊薄壁管等等。
4.承壓流體輸送用螺旋縫埋弧焊鋼管(SY/T5037-2000)是以熱軋鋼帶卷作管坯,經常溫螺旋成型,用雙面埋弧焊法焊接,用于承壓流體輸送的螺旋縫鋼管。鋼管承壓能力強,焊接性能好,經過各種嚴格的科學檢驗和測試,使用安全可靠。鋼管口徑大,輸送效率高,并可節約鋪設管線的投資。主要用于輸送石油、天然氣的管線。
5.承壓流體輸送用螺旋縫高頻焊鋼管(SY/T5038-2000)是以熱軋鋼帶卷作管坯,經常溫螺旋成型,采用高頻搭接焊法焊接的,用于承壓流體輸送的螺旋縫高頻焊鋼管。
6.鋼管承壓能力強,塑性好,便于焊接和加工成型;經過各種嚴格和科學檢驗和測試,使用安全可靠,鋼管口徑大,輸送效率高,并可節省鋪設管線的投資。主要用于鋪設輸送石油、天然氣等的管線。
7.一般低壓流體輸送用螺旋縫高頻焊鋼管(SY/T5039-2000)是以熱軋鋼帶卷作管坯,經常溫螺旋成型,采用高頻搭接焊法焊接用于一般低壓流體輸送用螺旋縫高頻焊鋼管。
8.樁用螺旋焊縫鋼管(SY/T5768-2000)是以熱軋鋼帶卷作管坯,經常溫螺旋成型,采用雙面埋弧焊接或高頻焊接制成的,用于土木建筑結構、碼頭、橋梁等基礎樁用鋼管。
螺旋鋼管工藝流程
(1)原材料即帶鋼卷,焊絲,焊劑。在投入前都要經過嚴格的理化檢驗。
(2)帶鋼頭尾對接,采用單絲或雙絲埋弧焊接,在卷成鋼管后采用自動埋弧焊補焊。
(3)成型前,帶鋼經過矯平、剪邊、刨邊,表面清理輸送和予彎邊處理。
(4)采用電接點壓力表控制輸送機兩邊壓下油缸的壓力,確保了帶鋼的平穩輸送。
(5)采用外控或內控輥式成型。
(6)采用焊縫間隙控制裝置來保證焊縫間隙滿足焊接要求,管徑,錯邊量和焊縫間隙都得到嚴格的控
制。
(7)內焊和外焊均采用美國林肯電焊機進行單絲或雙絲埋弧焊接,從而獲得穩定的焊接規范。
(8)焊完的焊縫均經過在線連續超聲波自動傷儀檢查,保證了100%的螺旋焊縫的無損檢測覆蓋率。若有缺陷,自動報警并噴涂標記,生產工人依此隨時調整工藝參數,及時消除缺陷。
(9)采用空氣等離子切割機將鋼管切成單根。
(10)切成單根鋼管后,每批鋼管頭三根要進行嚴格的首檢制度,檢查焊縫的力學性能,化學成份,溶合狀況,鋼管表面質量以及經過無損探傷檢驗,確保制管工藝合格后,才能正式投入生產。
(11)焊縫上有連續聲波探傷標記的部位,經過手動超聲波和X射線復查,如確有缺陷,經過修補后,再次經過無損檢驗,直到確認缺陷已經消除。
(12)帶鋼對焊焊縫及與螺旋焊縫相交的丁型接頭的所在管,全部經過X射線電視或拍片檢查。
(13)每根鋼管經過靜水壓試驗,壓力采用徑向密封。試驗壓力和時間都由鋼管水壓微機檢測裝置嚴格控制。試驗參數自動打印記錄。
(14)管端機械加工,使端面垂直度,坡口角和鈍邊得到準確控制。
探傷標準:可按照中國(JB4730,GB/T2970)、美國(A435、A577、A588)、日本(JISG0801、JISG0901)、德國(SEL072)、英國(BS5996)、法國(NFS04-305)等國內外探傷標準生產檢驗。
3、管線管的生產工藝
目前在國內管線鋼的生產工藝主要有:常規半連續熱連軋、CSP連鑄連軋、中厚板機組、爐卷機組。
(1)半連續軋機:包括1機架爐卷軋機及5機架精軋機。在半連續軋機上,鋼帶在精軋道次所經歷的熱軋從鋼帶的一端到另一端實質上是恒定的。在精軋機上道次間的
時間通常少于3s。
(2)CSP連鑄連軋:在CSP生產線上對含有鈮、釩、鈦復合微合金化的低碳錳鋼,采用合適的控軋控冷和卷取工藝,可以保證鋼的力學性能和顯微組織符合現代X60管線鋼的技術要求,符合現代管線鋼發展趨勢。我國CSP連鑄連軋生產線目前已開發到了X60管線鋼,而美國及國外其它CSP生產廠已經開發和生產了高牌號管線鋼X60、X65乃至X70。
其工藝特點是連鑄薄板坯存在中心偏析,消除連鑄薄板坯中心偏析是進一步進步管
線鋼質量的關鍵技術題目。
(3)中厚板機組:主要生產寬厚板,用于直縫埋弧焊管的生產,直縫埋弧焊管質量可靠,廣泛應用于油氣高壓輸送主干線上。
(4)爐卷軋機:爐卷軋機包括一架往復式粗軋機及一架4輥往復精軋機。在精軋機兩邊的輸送線上安裝了兩臺熱卷軋機。輸出輥道通常包括一套層流冷卻系統和一個卷取站。在爐卷軋機上,鋼帶整個長度上的熱機械歷史明顯變化,尤其是在微合金化鋼生產中,將強烈影響精軋機上產生的再結晶程度、晶粒長大及析出,并且導致整個帶鋼長度上終極顯微組織和性能的劇烈變化。其工藝特點是投資本錢相對低。
目前國外在爐卷生產線上已生產出X70、X80級管線鋼,主要生產廠家為IPSCO,該廠具有超過35年操縱爐卷軋機的經驗,近年來已對550MPa級Ⅱ類的1219mm直徑及12.0mm壁厚管線鋼進行了產業生產。
焊接鋼管按工藝區分主要有電阻焊(ERW)、螺旋埋弧焊(SSAW)和直縫埋弧焊(LSAW)三種工藝。這三種工藝生產的焊管,因其原料、成型工藝、口徑大小以及質量的不盡相同,在應用領域里各有定位。
(a)直縫電阻焊管(ERW)
電阻焊管是我國最早生產、應用范圍最廣、生產機組最多(2000余家)、產量最高(占焊管總產能的80%左右)的鋼管品種,產品規格為φ20~610mm,在國民經濟建設中發揮了重要作用。ERW219-610mm機組自20世紀80年代以來,約有30余套是從國外引進的較先進技術。經過多年生產實踐,裝備技術水平又有較大進步,產品質量也在不斷改善。因其投資少,見效快,應用范圍廣而發展迅猛。隨著板材CSP生產工藝的發展,為其提供了低本錢、質量可靠的原料,并為其今后進一步發展創造了良好的條件。這部分產品已由流體輸送、結構領域向無縫管應用領域的油井管、管線管發展。其典型生產工藝流程應為:板帶原料→原料預處理→冷彎成型→焊接→焊縫熱處理→焊縫(管體)探傷→精整→成品焊管。
(b)螺旋埋弧焊管(SSAW)
螺旋埋弧焊管設備投資較少,因采用價格較低的窄帶(板)卷連續焊接生產大口徑(φ1016~2400mm)焊管,生產工藝簡單、運行用度低,具有低本錢運行上風。目前,我國油氣輸送螺旋焊管已形成了以石油系統所屬鋼管廠為主的基本格式。采用低殘余應力成型和管端機械擴徑等先進技術,經過嚴格質量控制的螺旋焊管在質量上可與直縫焊管相媲美,我國西氣東輸等油氣長輸管道工程中獲得了廣泛應用,是我國油氣長輸管道工程采用的主要管型。其目前的產能已經能夠滿足我國油氣長輸管道工程建設的需要,并已大量出口。
(c)直縫埋弧焊管(LSAW)
直縫埋弧焊在我國事較晚發展起來的先進制管技術,過往主要采用UOE技術制造。
近年來漸進式JCOE在我國和全世界逐漸成為另一種新的主流技術。直縫埋弧焊管質量可靠,廣泛應用于油氣高壓輸送主干線上。該焊管機組由于投資相對較大,使用的原材
料為本錢較高的單張寬厚板,工藝較復雜,生產效率低,產品本錢較高。
由于我國高壓油氣輸送管線每年需要大中口徑焊管100萬t左右,主要采用螺旋焊管,直縫埋弧焊管將作為螺旋焊管的補充,主要應用于螺旋焊管機組不能生產的大壁厚鋼管(17.5mm以上)和彎管用母管,其用量受到一定限制
目前,我國油氣輸送所使用的管線管主要由石油自然氣團體公司的6個焊管廠生產,它們是寶雞石油鋼管廠、貴陽石油鋼管廠、華北石油鋼管廠,遼陽石油鋼管廠,沙市石油鋼管廠,勝利石油鋼管廠等,總設計生產能力約為120萬t左右。生產的油氣管以螺旋焊管和高頻直縫焊管為主,而管徑大、管壁厚的直縫埋弧焊管的生產在我國時間較短。2000年,我國第一條大口徑直縫埋弧焊管生產線在番禺珠江鋼管公司建成,此生產線從澳大利亞引進,可生產厚壁大口徑長輸管線鋼管,鋼管外徑457~1800mm,特殊規格可達3000mm,壁厚4.5~37mm,特殊規格還可增厚,單管最長可達12m。但生產這種焊
管所需管線用寬厚鋼板目前基本還需依靠進口。近日,日本住友金屬和住友商事又與中國石油自然氣團體公司(CNPC)下屬的寶雞鋼管廠合作生產石油自然氣用中徑焊接鋼管,主要生產油氣輸送管線的支線用焊管,產量可由目前的5萬t進步到2~3年后的12萬t。
5、管線鋼的發展趨勢
油氣管道特別是天然氣管道發展的一個重要趨勢是采用大口徑、高地、壓富氣輸送、高寒和腐蝕服役環境、海底管道厚壁化及選用高級別管材。考慮到管道的結構穩定性和安全性,還需增加管壁厚度和進步管材的強度,因此用作這類輸送管的管線鋼都向著厚規格和高強度方向發展。采用高壓輸送和高強度管材,可大幅度節約管道建設成本。目前,輸氣管道的設計和運行壓力已達20MPa,有些管道甚至考慮采用更高的壓力。隨著管道輸送壓力的不斷提高。管線鋼管也迅速向高鋼級發展。因此對鋼材質量要求也日益苛刻,在成分和組織上要求鋼材向著“超高純、超均質、超細化”方向發展。
由于自然氣的可壓縮性,因而輸氣管的輸送壓力要較輸油管為高。近年來國外多數輸氣管道的壓力已從早期的4.5~6.4MPa進步到8.0~12MPa,有的管道則達到了14~15.7MPa,從而使輸氣管的鋼級也相應地進步。目前,國外的大口徑輸氣管已普遍采用X70鋼級,X80開始進進小規模的使用階段,X100也研制成功,并著手研制X120。
21世紀是我國輸氣管建設的高峰時期。“西氣東輸”管線采用大口徑、高壓輸送管的方法。這條管線全長4167km,輸送壓力為10MPa,管徑為1016mm,采用的鋼級為X70、厚度為14.6mm,20℃的橫向沖擊功為≥120J。這一鋼級、規格、韌性級別目前國內已經生產,并且質量達到國際水平。因此,生產這種規格的高強度、高韌性管線鋼對我國今后采用國產管線鋼生產大口徑、高壓輸氣管具有十分重大的戰略意義。
大口徑高壓輸送及采用高鋼級管材是國際管道工程發展的一個重要趨勢:
(1)國內對管線用鋼的需求以X70級為主,新線目標定位在X80級熱軋寬鋼帶和X100級寬厚板的生產,以適應目前10MPa和近期14MPa以上輸送壓力的設計。
(2)今后輸送的自然氣不再是經脫水、脫H2S處理的“甜氣”,而將是未經處理的“富氣”(PH2S≤300Pa),為此必須進步管線用鋼的抗氫致開裂和抗H2S應力腐蝕的性能。
(3)國內已具有70萬t以上螺旋焊管的制管能力,但大口徑直縫埋弧焊管的產能和質量還不能滿足工程的需求,繼續部分進口成品管將不可避免。從研發基礎和生產技術的難度而言,具有優質的抗H2S應力腐蝕性能的高強度等級管線用鋼的開發應當列為科技攻關的重中之重。